Faq’s
Common Questions
What types of products do you have?
We are mainly engaged in three kinds of laser products: laser cleaning machines, laser marking machines, and laser welding machines.
There are the categories:
- Laser cleaning machine: We currently supply standard handheld type pulsed laser cleaner with optional power 50W/60W/80W/100W/200W/350W/500W; 1000w, 1500w, 2000w, 3000w handheld continuous laser cleaning machines; We can also equip with fixture or robotic arm to achieve an automatic cleaning line. In addition, we have backpack-type laser cleaners 100W and 150W and Pull rod-type 200W laser cleaning machines, especially for outdoor cleaning.
- Laser marking machine: fiber laser marking machine, 3D dynamic fiber laser marking machine, fiber large working-field laser marking machine(up to 700*700*80mm), CO2 laser marking machine, CO2 large working-field laser marking machine(up to 1200*1200*100mm), UV laser marking machine, green laser marking machine and UV laser marking machine are all available to fulfill no matter what the marking/engraving applications customers may have. Moreover, we provide customizing functions such as rotating tools, 2D/XYZ marking slide, visual localization marking, offline marking, zoom-in display, online flying marking, etc, according to customers’ actual needs and requirements.
- Laser welding machine: we mainly supply 1000w、1500w、2000w and 3000w hand-held welding machines; and Galvanometer laser welding machines (for high efficiency off-line/on-line welding of precision laser spot welding, overlapping welding, sealing welding of various micro parts)
How shall I choose the optimum machine for me?
First of all, you may want to inform us:
- About laser cleaning machine: What industry is it used for? The substrate of the object to be cleaned, the surface material to be removed, and its thickness? Would you mind providing sample pictures or videos? Would you like to send us some samples for further testing?
- About the laser marking machine: What is the marking material? Size of the marking field? Is there a specified laser power? The shape of the object? Is there any requirement for marking depth? Does it require an assisting tool?
- About laser welding machine: What is the welding material? Aluminum, stainless steel, galvanized sheet, or else? The thickness of the welding material? Laser power?
- Do you have a purchase budget? Is a pre-sales proofing test required? We will recommend the most suitable products to you according to your budget and cleaning/marking/welding requirements.
This is my first time to buy this kind of machine. Is it easy to use?
The operation is very simple. Most of our customers mastered the use skills within one single hour. We will send you the English version(the language is customized) of the user manual and operation guiding video, as well as we can train you through remote online video chatting.
How long is the delivery time usually?
7-10 days for standard equipment and 15-30 days for customizing types after the payment is confirmed.
What kind of package do you use?
Wooden box or flight case with wheels, which are safe and suitable for international transportation.
How do you guarantee the quality of the goods?
Each equipment of shall experience a strict quality inspection and long-time continuously running test(72 hours) before shipping out. We provide inspection videos or photos for customers to confirm the marking/cleaning effects and performance of our machine. A quality certificate and warranty card will be sent along with the package.
How can you guarantee the delivery time?
Is there any consumables or necessary accessories during the usage?
There will not be any consumables or accessories for using our machine. Electricity is the only fuel. The accessories shall be sent along with the machines(free of charge):
- For the laser marking machine: one USB (with correction parameters), one steel ruler, one set of inner hexagon wrenches, USB connection cable for the controller. (Note: Laser protection goggles are optional for 50usd/set.)
- For laser cleaning machine: one USB to serial port RS232 connection cable, 1 piece laser protection goggles, one set of inner hexagon wrench, protective lenses (Note: 2 pieces of lens for 200W and below, 3 pieces of lens for above 200W).
- For laser welding machine: one USB to serial port RS232 connection cable, 1 piece laser protection goggles, one set of inner hexagon wrench, 1 Wire feeder (including 1.0 steel wire 5kg), one set of copper nozzle, protective lenses 10 pieces.
Could I have some further discount?
There are two most important factors to distinguish prices: 1. product quality and 2. after-sales service.
- Low-price products are prone to quality problems. In order to seize the market, manufacturers or trading company set the sales price very low to win customers. So if they want to make profits when selling at a low price, they can only reduce production costs and labor costs, such as purchasing components from Small workshops without any quality assurance, and even using second-hand lasers, galvanometer systems, pirated controller boards, and other core accessories. Therefore problems keep coming with unstable performance or short service life, which may cause a lot of issues for users. In addition, the manufacturer reduces the labor cost, which will also lead to problems such as loose assembly process, disordered internal wiring, no quality inspection before shipping, rough packaging, etc.
- After-sales service, it’s very difficult to support high-quality service when there is not enough profit. Technical support cannot keep up, the after-sales service is slow and not available timely due to profits limitations. Not to mention the necessary consumables such as protective lens and goggles cannot be provided when using the equipment, which may cause potential safety problems for the users also. There are many cases that the supplier cannot be contacted after technical problems occur
- Our products are positioned in the middle and high-end market of customized development. We select the core parts and genuine components of reliable manufacturers to ensure the performance and quality of the whole machine. At the same time, for the technology and process of internal production, we are rigorous, standardized, and will go through a long-time running test before a machine is shipped out. The quality inspection report will be provided with a solid and durable (wooden box or air box)package. We will monitor the status of logistics transportation to ensure that the goods shall be safely and timely delivered to customers.
- Meanwhile, we provide thoughtful and timely online after-sale technical services. The company implements 7*24 hour global service response and provides life-long technical maintenance services for our machines. Free repair and replacement services are also available according to the warranty terms until the customer’s problems are solved and the customer is satisfied.
- Therefore, for the same kind, our products have more reliable quality, better service and are much more cost-effective for buyers. And of course, in view of your application and requirements, I will try my best to apply to the company leaders for a better price for you, thanks for your trust.
What payment terms should be acceptable?
100% payment before shipment and multiple payment methods are acceptable.(Wire transfer, Alibaba, Paypal, and credit cards )
Note: 20%-30% advance payment and 70% final payment before shipping the machine are acceptable for evaluated clients. Other terms of payment are negotiable for evaluated agents.
What's your warranty period?
The two-year warranty period for all laser machines. Technical support and services are lifetimes available (warranty of the laser source depends on the brand and its category).
What is your after-sales service?
24-hour online service, with video instruction & guidance, and technical training, which are lifelong available for free. Any repairing or replacing under warranty terms will be free of charge. Our company can also provide door-to-door service if required. If there is a quality failure with the laser source within three months of receiving the goods, it will be replaced free of charge.
What technical support can be provided?
24-hour online technical support is provided, such as Q & A, equipment operation, maintenance, replacement, and other operation guidance. Besides, pre-sale testing, on-site demonstration, and automatic processing scheme designing are also available.
What qualifications does your company possess?
We are a certified national high-tech enterprise, “MRJ-LASER/迈锐捷” is the national registered trademark. The company owns more than 30 patent certifications(2 international patents for the core technology of high-power laser cleaning applications in the United States and Europe). All products have passed CE and FDA certifications.
What are your advantages over all the competitors?
- Our company has been engaged in the laser industry for 12 years. With a first-class R&D team, we focus on customizing and intelligent laser marking/cleaning/ welding, etc. Combined with deep research in laser source, control software, galvanometer scanner, automatic processing, etc.
- There are more than 30 engineers serving our customers, including mechanical designers, hardware engineers, software programmers, electrical engineers, laser application engineers, automation engineers, etc. to provide optical design, appearance design, software development, new application development, and other R&D support.
- Unique new products are launched to the market with patent rights every year.
- For special applications and customization needs, customers shall be invited to China to process cooperative research and development with our R&D team.
- Compared with the peer large companies, MRJ-Laser has the highest cost performance and better service: MRJ-Laser focuses on customized laser cleaning and laser marking at lower prices and is more professional. Comprehensive pre-sales, sales, after-sales technical support, and after-sales service more positive, thoughtful, faster response, and we are more professional in the laser cleaning subdivision field. (Big companies do more complex products, more comprehensive, and high prices, poor service attitude).
- Compared with the peer small companies, MRJ-Laser has more comprehensive strength: MRJ-Laser owns the core laser control technology, can do a full range of customized development, comprehensive technical strength is stronger. (Other small companies are generally engaged in assembly production, and all parts can only be purchased, without technical capability and quality guarantee. Most of them are engaged in one-shot trading. Although the price is low, there is no product quality and after-sales technical guarantee).
Can you provide customized services or laser processing automation solutions?
MRJ-Laser specializes in intelligent lase equipment(marking/cleaning/welding) Customization. Our professional R&D team will provide you with a full set of customizing services such as optical path, machinery, circuit control, automation, software, and hardware systems.
In which countries do you have agents?
At present, our products have been sold to more than 70 countries around the world, and we have agents in 14 countries around the world. For the specific distribution, please consult the relevant sales managers.
- General agents 9: USA, Canada, Germany, France, Spain, Norway, Hungary, Serbia, Iran
- Exclusive agents 5: Japan, Indonesia, Saudi Arabia, Denmark, Croatia.
Can I represent your products?
Yes, absolutely. For agents, our company will provide comprehensive cooperation and support. We have two types of agency: exclusive agency and non-exclusive agency. If you are interested in representing our products, please contact the relevant sales manager for further cooperation plan.
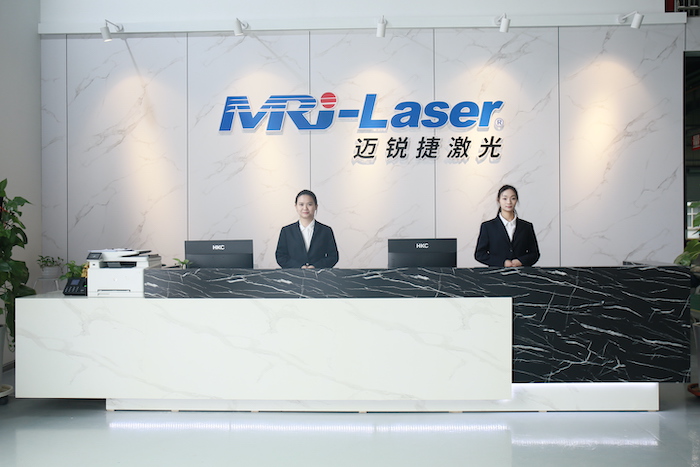
You still have questions ?
Is there any query left? You can directly share with us and clear away all your confusions.
Our Products On Sale
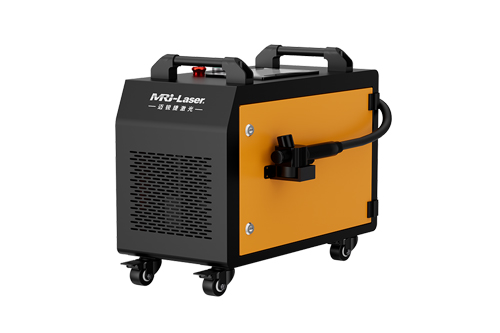
Mini 200W Handheld Pulse Laser Cleaner
01
Lightweight powerhouse for all your cleaning needs! Weighing in at just 36kg, this portable marvel is your versatile and efficient cleaning solution. It tackles it all effortlessly from oil stains to thick paint, heavy rust to stubborn grime. Discover cost-effective cleaning like never before!
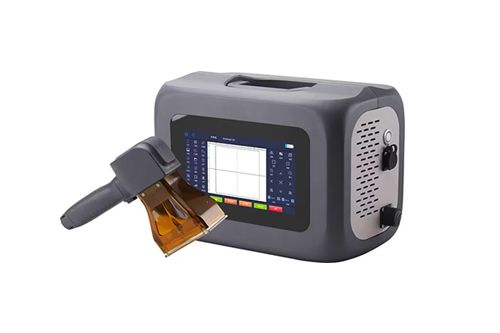
Mini Battery Handheld Fiber Laser Marking
02
This little powerhouse comes in two versions: one with a lithium battery and another that you can plug in. It’s super portable, weighing only 9.7kg for the whole unit and 0.9kg for the handheld part. Plus, the battery can last up to four hours, so you can work without interruptions.
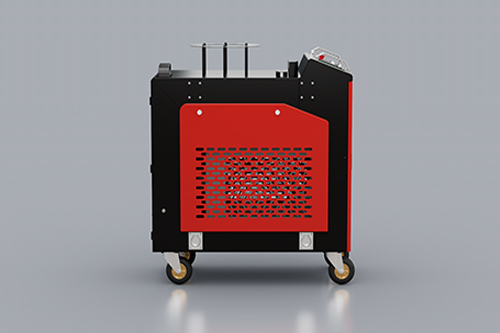
3000W CW Laser Cleaner
03
This laser cleaner has a handheld design, eight cleaning modes, and can be paired with an automated robotic arm, and 3000W of high power can efficiently complete the removal of paint from large steel structures, and the removal of paint from wall surfaces.